Project Background
When our client, a key player in the mining industry, faced excessive downtime and operational inefficiencies with their primary gyratory crusher, they turned to EARTHRES for a solution. Their existing primary gyratory crusher was causing unforeseen challenges that threatened to disrupt their operations. EARTHRES conducted a thorough analysis, specified a new primary Gyratory crusher, and provided comprehensive support. The result was significantly reduced downtime, increased efficiency, and a more stable operation.
The Challenge
The primary gyratory crusher being used was a relatively new model, one of only three in the world. Despite its novelty, it was plagued with several critical issues that impacted overall productivity and efficiency:
- Excessive Downtime: The crusher experienced frequent unscheduled downtime, causing significant operational delays.
- Manufacturer Support: There was inadequate support from the manufacturer, leading to prolonged periods without necessary parts and services.
- Capacity Mismatch: The crusher's capacity far exceeded what the pit could support, resulting in the crusher running empty much of the time.
- Maintenance Access: Poor maintenance access led to excessive downtime for repairs, further compounding operational inefficiencies.
- Structural Vibrations: The primary structure vibrated excessively, causing issues with the operator’s shack and control systems.
- Drive Arrangement Failures: The direct drive arrangement failed multiple times due to structural movement, necessitating outside contractor assistance for accurate motor alignment.
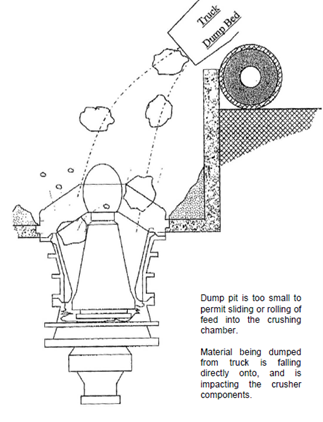
The Solution
Comprehensive Analysis and Planning
EARTHRES began by performing a detailed investigation of the existing conditions. This included observing equipment operation, gathering field measurements, and comparing them to as-built drawings. A series of steps were then undertaken to ensure the best possible solution:
1. Equipment Assessment:
- Determined the best type of crusher for the application.
- Evaluated potential manufacturers and local dealers for support.
- Ensured commonality of equipment within the organization.
- Assessed the familiarity of onsite personnel with the chosen equipment.
2. Selection of Replacement Crusher:
- Assessed jaw, gyratory, and impactor crushers and the desired capacity for the plant operations.
- Selected a manufacturer and model that met all the requirements and was more familiar to the client.
- Required minimal modifications to integrate into the existing facility minimizing project cost.
3. Site Inspection and Structural Analysis:
- Conducted a detailed site inspection to confirm dimensions and identify stress cracks in the existing structure.
- Created 3D drawings to integrate the new crusher into the current setup.
- Modified the design to the dump hopper to optimize the crusher feed arrangement.
4. Bid Preparation and Execution:
- Defined project milestones, ensuring a clear timeline for each phase of the project.
- Determined an opinion of probable cost and project timeline.
- Developed a bid package for steel fabrication, concrete installation, mechanical removal, and installation of the new crusher.
- Acted as the client’s representative to provide construction oversight and Construction Quality Assurance (CQA) support.
- Provided final commissioning support.
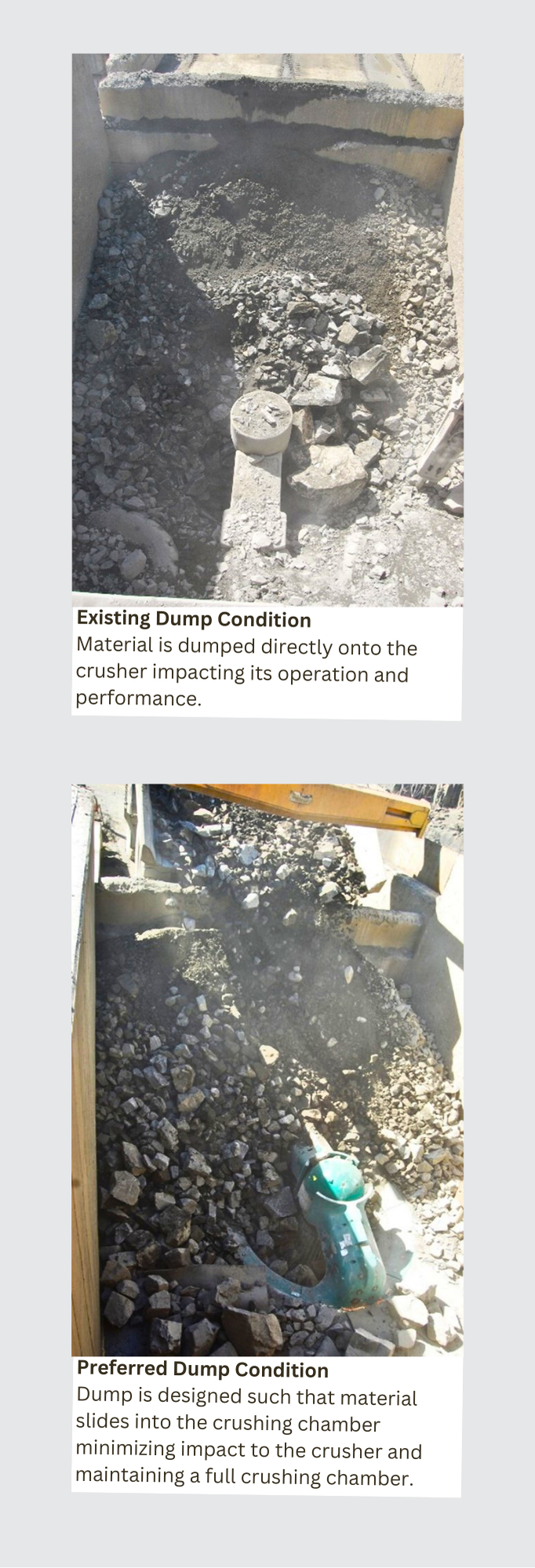
The Results
The implementation of the new crusher, along with comprehensive support from EARTHRES, brought significant benefits to the client:
-
Reduced Downtime: The new crusher’s design and installation minimized unscheduled downtime, allowing for continuous operations.
-
Enhanced Efficiency: Replacing an 800 hp crusher with a 500 hp crusher not only increased efficiency but also contributed to operational stability.
-
Improved Safety and Maintenance with 360° access to all levels of the Crusher: The original design had no provision for maintenance access below the crusher except through a manhole into a confined space.
Enhancing access to the crusher through the use of a removable rolling platform and new fixed platforms facilitated efficient and safer maintenance while reducing repair times and costs.
-
Increased Production Rate: The average production rate increased from 1200 TPH to 2000 TPH, demonstrating a marked improvement in throughput.
-
Operational Cost Savings: Operational improvements eliminated the need for a 2nd shift, significantly reducing annual operating costs.
-
Return on Investment: The project achieved ROI in only 2 years, which is half of the normal ROI for a project of this nature.
-
Operational Stability: The upgraded drive arrangement and structural reinforcements minimized failures and the need for outside contractor intervention.
EARTHRES’ Mining Engineering Consulting services provided thorough analysis, strategic planning, and expert execution to overcome significant operational challenges. By implementing the process solution and providing ongoing support, they enabled their client to achieve greater efficiency and stability in their operations.
EARTHRES continues to collaborate with this client to find innovative solutions to further optimize their processes and achieve new levels of operational excellence.
Click the links to learn more about our Mining Process Plant Design and our Mining Operations & Maintenance Support Services.
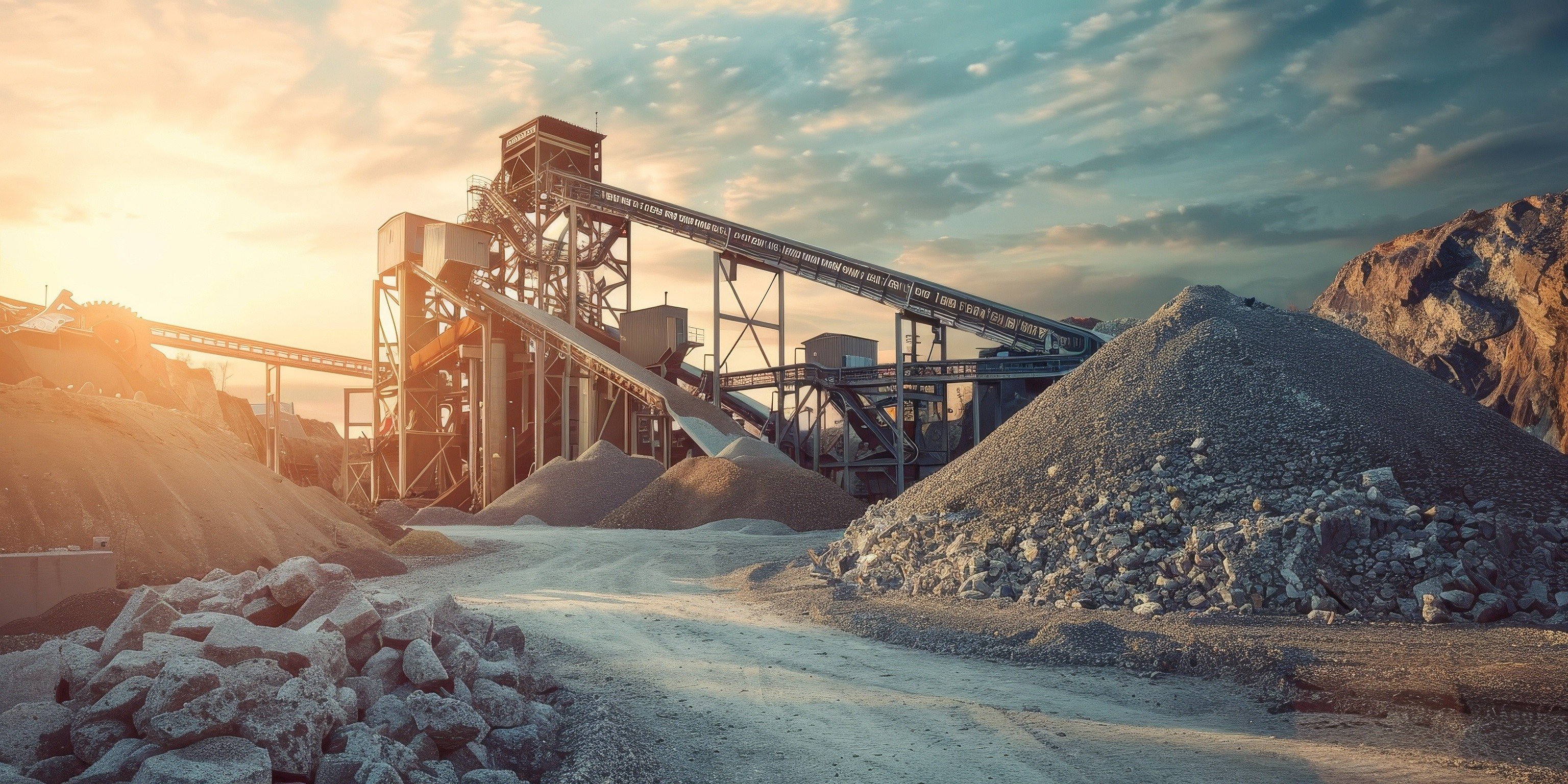
Have a similar challenge?
Let us help you! Get in touch with us today.