Project Background
When our client, a leading mining company, struggled with underutilization of their sand plant, they sought out EARTHRES for a solution. The plant, operating at only 36% capacity, relied on haul trucks and loaders, causing inefficiencies. EARTHRES conducted a thorough assessment and designed a reclaim and conveyor system to streamline the feeding process, boosting operational efficiency and eliminating the need for heavy equipment. The result was a dramatic increase in production, reduced fuel consumption, and faster return on investment, delivering significant long-term benefits for the client.
The Challenge
While on a site visit for a primary crusher renovation project, our engineering team noticed the inefficiency of the sand plant operation.
The mining company fed the sand plant from a surge pile using one (1) 980-loader and two (2) 40-ton haul trucks. As the sand plant was designed to operate with a steady feed rate of 700 TPH, feeding the sand plant with only the trucks yielded a drastically under-utilized production rate of 250 TPH or 36% of capacity.
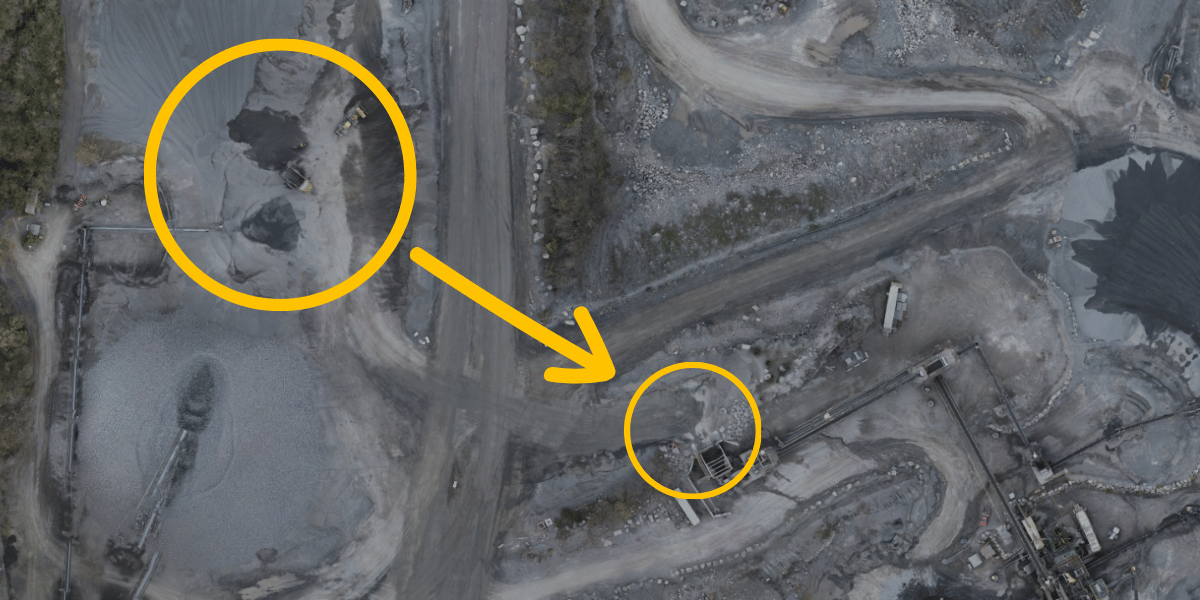
The Solution
After evaluating operating cost of the loader and trucks and confirming the design capacity of the sand plant to be 700 TPH, EARTHRES developed a conceptual design of a reclaim and conveyor system to continuously feed the sand plant directly from the surge pile with an adjustable feed rate of up to 800 TPH eliminating the need for the loader and trucks.
The ROI Analysis showed 6 months full payback if operating the sand plant at a feed rate of 600 TPH.
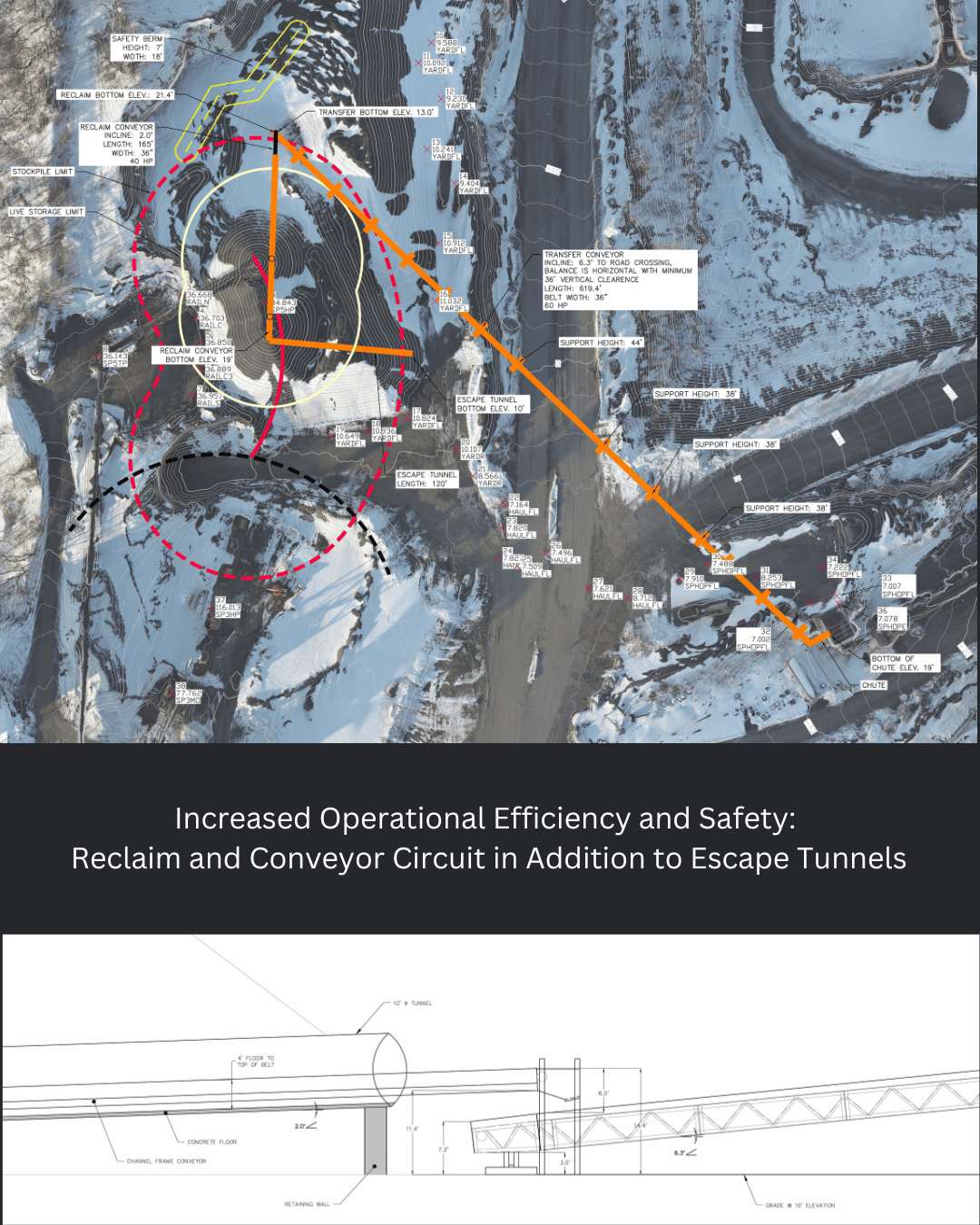
The Results
Implementation of the new Reclaim and Conveyor Circuit as designed along with comprehensive support from EARTHRES brought significant benefits to the client:
- Increased Production Rate: The production rate increased from an actual 250 TPH to a design potential of 800 TPH. Actual operations have been running at 650 TPH on average.
- Return on Investment: In the design phase, an ROI Analysis showed full payback in 6 months; however, once installed and operating, the actual payback time was only 4 months!
- Reduced Fuel Usage: In eliminating the vehicular use to feed the sand plant, the vehicle miles traveled, emissions, over 100,000 gal/yr of fuel were no longer needed to transfer sand from the surge pile to the feeder.
- Reduced Power Usage: The total power usage for the Sand Plant Operation was reduced by 1,046 HP.
- Reduced Carbon Footprint: Greenhouse gas (GHG) emissions were reduced by over 1,055 TPY.
EARTHRES’ Mining Engineering Consulting services provided thorough analysis, strategic planning, and expert execution to overcome significant operational challenges. By implementing the process solution and providing ongoing support, they enabled their client to achieve greater efficiency and productivity from their operations.
EARTHRES continues to collaborate with this client to find innovative solutions to further optimize their processes and achieve new levels of operational excellence.
Click the links to learn more about our Mining Process Plant Design and our Mining Operations & Maintenance Support Services.
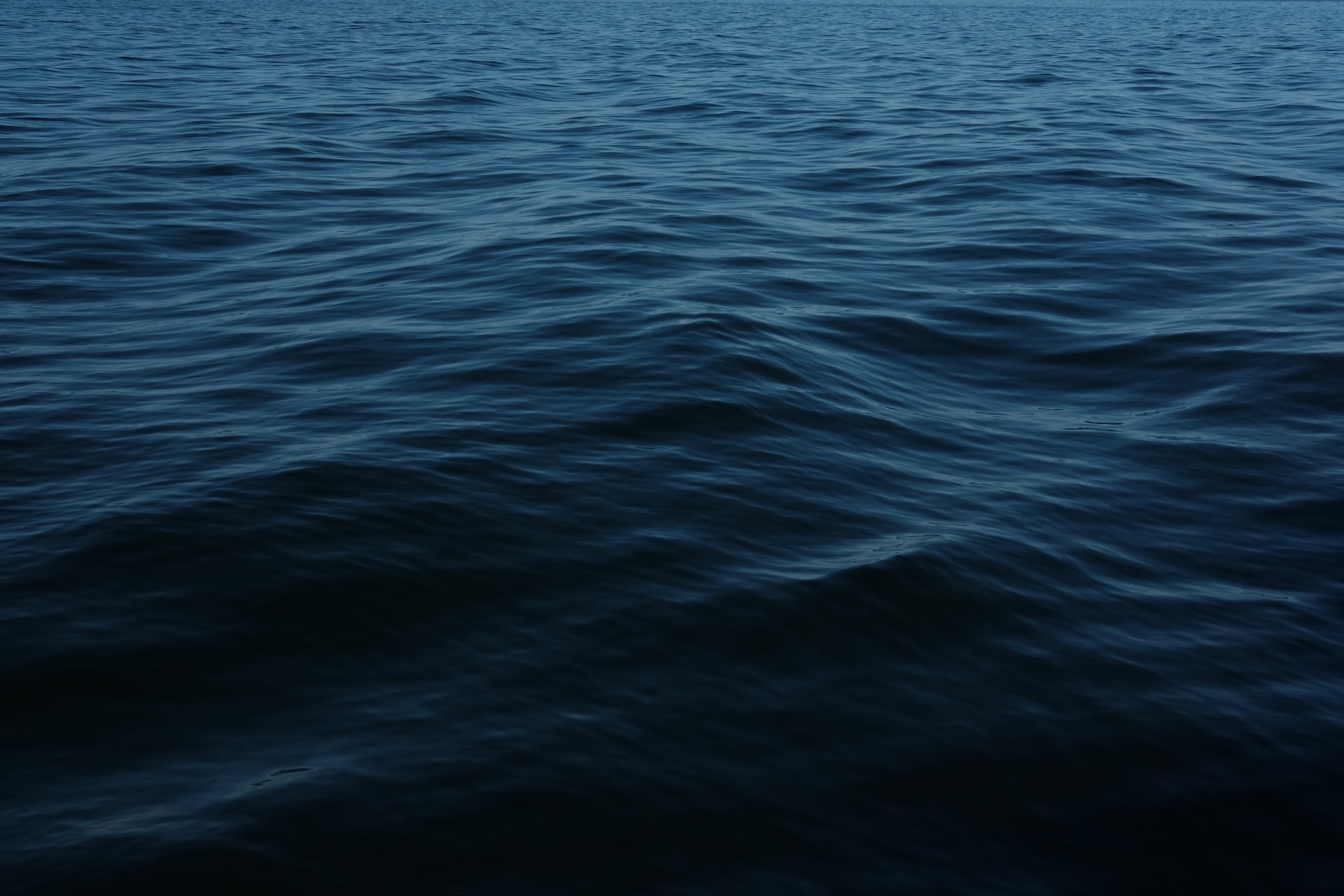
Have a similar challenge?
Let us help you! Get in touch with us today.